Comprehensive Guide: What is Porosity in Welding and Exactly How to avoid It
Wiki Article
The Science Behind Porosity: A Comprehensive Overview for Welders and Fabricators
Understanding the detailed mechanisms behind porosity in welding is important for welders and fabricators pursuing impeccable workmanship. As metalworkers look into the midsts of this sensation, they uncover a globe governed by different aspects that influence the formation of these small gaps within welds. From the composition of the base materials to the intricacies of the welding procedure itself, a plethora of variables conspire to either exacerbate or minimize the visibility of porosity. In this comprehensive overview, we will unravel the scientific research behind porosity, discovering its impacts on weld high quality and unveiling advanced techniques for its control. Join us on this journey via the microcosm of welding blemishes, where precision fulfills understanding in the quest of flawless welds.Comprehending Porosity in Welding
FIRST SENTENCE:
Assessment of porosity in welding discloses crucial insights right into the stability and quality of the weld joint. Porosity, defined by the visibility of tooth cavities or voids within the weld metal, is a common problem in welding procedures. These voids, if not properly resolved, can endanger the structural honesty and mechanical residential or commercial properties of the weld, causing prospective failures in the completed product.
To detect and evaluate porosity, non-destructive testing methods such as ultrasonic testing or X-ray evaluation are commonly utilized. These methods permit the recognition of inner defects without compromising the stability of the weld. By assessing the dimension, form, and circulation of porosity within a weld, welders can make educated decisions to boost their welding procedures and accomplish sounder weld joints.

Aspects Affecting Porosity Development
The event of porosity in welding is influenced by a myriad of aspects, ranging from gas protecting performance to the complexities of welding specification setups. Welding parameters, consisting of voltage, current, travel rate, and electrode kind, also influence porosity formation. The welding technique utilized, such as gas metal arc welding (GMAW) or secured metal arc welding (SMAW), can affect porosity formation due to variants in heat circulation and gas coverage - What is Porosity.Impacts of Porosity on Weld High Quality
Porosity formation significantly jeopardizes the architectural integrity and mechanical residential or commercial properties of bonded joints. When porosity is present try these out in a weld, it produces spaces or dental caries within the product, reducing the overall stamina of the joint. These gaps work as stress and anxiety concentration points, making the weld more vulnerable to breaking and failing under lots. The visibility of porosity additionally damages the weld's resistance to deterioration, as the trapped air or gases within the voids can respond with the surrounding setting, bring about destruction with time. In addition, porosity can prevent the weld's capacity to hold up against stress or effect, additional endangering the overall quality and reliability of the bonded framework. In essential applications such as aerospace, auto, or architectural buildings, where security and sturdiness are critical, the harmful effects of porosity on weld top quality can have serious repercussions, emphasizing the importance of reducing porosity through correct welding methods and procedures.Methods to Decrease Porosity
In addition, using the suitable welding criteria, such as the proper voltage, existing, and take a trip rate, is critical in preventing porosity. Preserving a constant arc length and angle during welding also helps reduce the possibility of porosity.
Using the ideal welding strategy, such as back-stepping or utilizing a weaving motion, can additionally assist disperse warm equally and reduce the opportunities of porosity formation. By implementing these strategies, welders can successfully minimize porosity and create top quality bonded joints.
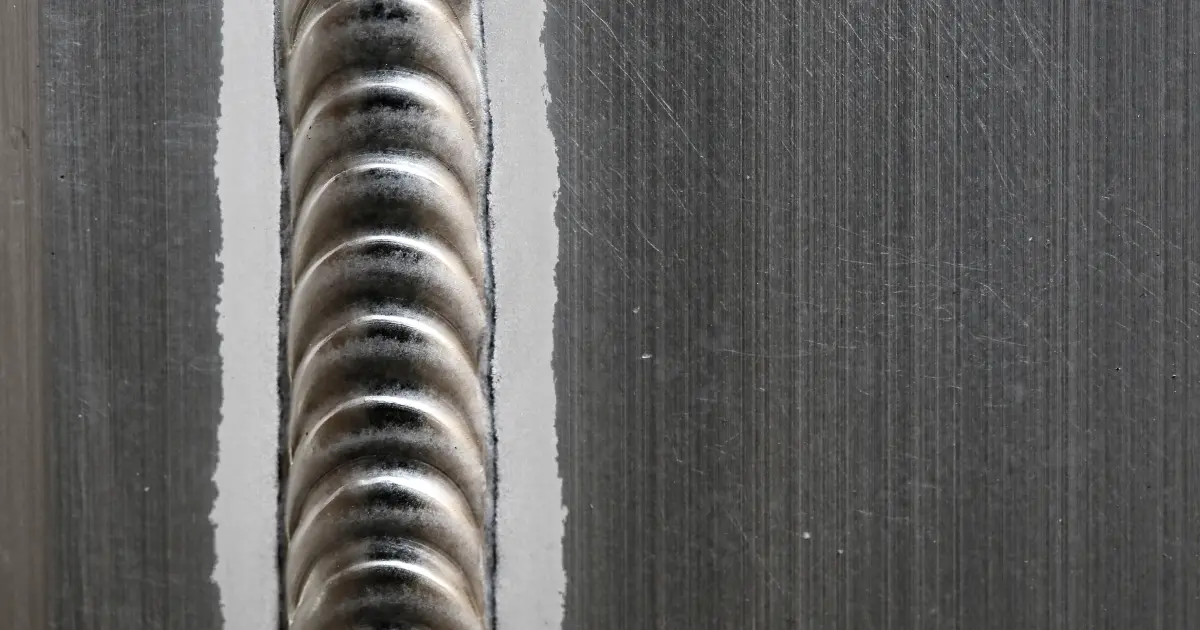
Advanced Solutions for Porosity Control
Implementing innovative innovations and cutting-edge methods plays a pivotal role in accomplishing superior control over porosity in welding processes. Furthermore, utilizing innovative welding techniques such as pulsed MIG welding or customized ambience welding can also assist find more information alleviate porosity concerns.Another sophisticated option entails the use of advanced welding devices. As an example, utilizing tools with integrated attributes like waveform control and advanced power sources can improve weld quality and decrease porosity dangers. Moreover, the implementation of automated welding systems with precise control over parameters can substantially lessen porosity defects.
Moreover, integrating sophisticated monitoring and evaluation technologies such as real-time X-ray imaging or automated ultrasonic testing can assist in identifying porosity early this article in the welding procedure, enabling for instant restorative actions. Overall, incorporating these innovative options can significantly improve porosity control and boost the general quality of bonded parts.
Verdict
In final thought, understanding the scientific research behind porosity in welding is important for welders and makers to create top quality welds - What is Porosity. Advanced solutions for porosity control can better boost the welding process and ensure a solid and trustworthy weld.Report this wiki page